在焊接不銹鋼盤管時,避免出現(xiàn)氣孔和裂紋需要從多個方面進行考慮和操作。以下是具體的方法:
避免氣孔的方法
焊接材料的選擇與處理
選用高質(zhì)量的焊接材料:選擇合適的焊條、焊絲和保護氣體至關重要。對于不銹鋼盤管焊接,應根據(jù)母材的化學成分和性能要求,挑選與之匹配的焊接材料。例如,對于奧氏體不銹鋼,使用含有穩(wěn)定化元素(如鈮、鈦)的焊絲可以減少氣孔產(chǎn)生的可能性。同時,焊接材料要確保質(zhì)量合格,無受潮、氧化等問題。
嚴格的烘干和清潔處理:焊條和焊劑使用前應按照規(guī)定進行烘干。例如,低氫型焊條烘干溫度一般在350-400℃,保溫時間1-2小時,以其中的水分。焊絲表面如有油污、鐵銹等雜質(zhì),要進行清潔處理,可使用有機溶劑(如丙酮)擦拭或采用機械打磨的方式。
焊接環(huán)境控制
控制濕度和清潔度:焊接環(huán)境的濕度應盡量保持在較低水平,一般建議濕度不超過60%。在濕度較大的環(huán)境下,空氣中的水分容易進入熔池,形成氣孔。同時,要確保焊接區(qū)域清潔,避免灰塵、油污等雜質(zhì)混入焊接熔池??梢栽诤附蝇F(xiàn)場設置防風、防塵設施,如搭建簡易的焊接棚。
保護氣體的正確使用:在采用氣體保護焊(如氬弧焊)時,保護氣體的純度和流量對防止氣孔至關重要。氬氣純度一般要求在99.99%以上。氣體流量應根據(jù)焊接電流、焊接速度和噴嘴尺寸等因素合理調(diào)整。例如,焊接電流為100-150A時,氬氣流量可控制在8-12L/min。同時,要確保保護氣體能夠地覆蓋焊接區(qū)域,噴嘴與焊件的距離保持在合適的范圍內(nèi)(通常為8-14mm)。
焊接工藝參數(shù)優(yōu)化
控制焊接電流和電壓:焊接電流和電壓過高或過低都可能導致氣孔產(chǎn)生。電流過大時,焊接熔池溫度過高,金屬蒸發(fā)過快,容易卷入氣體形成氣孔;電流過小時,熔池攪拌不充分,氣體逸出困難。對于不銹鋼盤管焊接,應根據(jù)管材的厚度、焊絲直徑等因素合理調(diào)整電流和電壓。例如,在焊接1-3mm厚的不銹鋼盤管時,采用鎢極氬弧焊,焊接電流可控制在80-120A,電壓在10-14V。
合適的焊接速度:焊接速度過快,熔池存在時間短,氣體來不及逸出;焊接速度過慢,熔池過熱,也會增加氣孔產(chǎn)生的幾率。要根據(jù)管材的材質(zhì)和焊接工藝選擇合適的焊接速度。例如,在自動氬弧焊焊接不銹鋼盤管時,焊接速度可控制在10-30cm/min。
避免裂紋的方法
母材和焊接材料質(zhì)量控制
確保母材質(zhì)量合格:不銹鋼盤管母材應符合相應的質(zhì)量標準,避免使用有缺陷(如夾雜、偏析)的材料。在焊接前,要對母材進行檢查,包括化學成分分析、金相組織檢查等。對于有疑問的材料,可進行試焊和性能測試。
匹配的焊接材料:焊接材料的化學成分應與母材相匹配,特別是碳當量。過高的碳當量會增加焊縫的淬硬傾向,導致裂紋產(chǎn)生。例如,在焊接奧氏體不銹鋼時,選用碳含量較低的焊接材料可以降低熱裂紋的風險。同時,焊接材料的強度和韌性也要與母材相適應,避免因強度不匹配而產(chǎn)生裂紋。
焊接預熱和后熱
合理的預熱措施:對于一些易產(chǎn)生冷裂紋的不銹鋼材料或厚壁盤管,焊接前進行預熱可以降低焊縫的冷卻速度,減少焊接應力,從而避免裂紋產(chǎn)生。預熱溫度根據(jù)母材的材質(zhì)、厚度和焊接工藝等因素確定。例如,對于馬氏體不銹鋼厚壁盤管,預熱溫度可控制在150-300℃。預熱范圍一般為焊縫兩側(cè)各100-150mm。
適當?shù)暮鬅崽幚恚汉附雍髮讣M行后熱(如消氫處理)可以加速焊縫中氫的逸出,減少氫致裂紋的產(chǎn)生。后熱溫度一般在200-350℃,保溫時間根據(jù)焊件的厚度和焊接工藝等因素確定,通常為2-6小時。
焊接工藝控制
控制焊接熱輸入:焊接熱輸入過大,會導致焊縫和熱影響區(qū)過熱,晶粒粗大,增加裂紋產(chǎn)生的傾向。應根據(jù)管材的材質(zhì)和厚度,合理控制焊接電流、電壓和焊接速度,以控制熱輸入。例如,在焊接薄壁不銹鋼盤管時,采用小電流、高速度的焊接方式,以降低熱輸入。
采用合理的焊接順序和方向:對于復雜的不銹鋼盤管結(jié)構(gòu),合理的焊接順序和方向可以減小焊接應力。例如,采用對稱焊接、分段退焊等方法,使焊接應力分布更加均勻,避免應力集中導致裂紋產(chǎn)生。
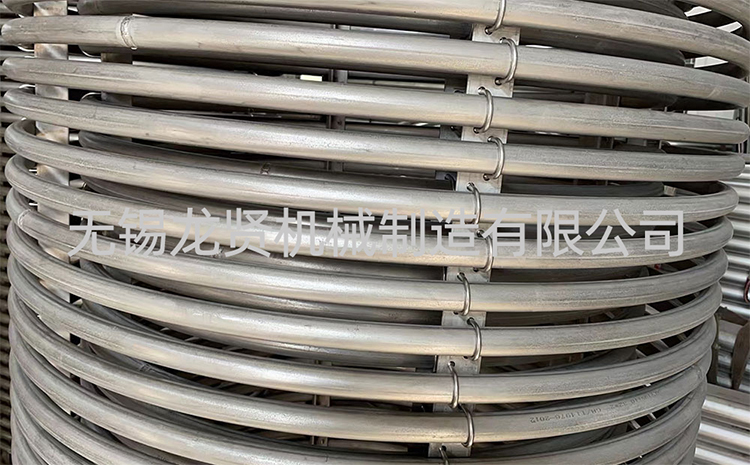
文章來源于:http://yiege.com/problem_detail.asp?id=594